Discover What is Porosity in Welding and Its Result on Structural Stability
Discover What is Porosity in Welding and Its Result on Structural Stability
Blog Article
Porosity in Welding: Identifying Common Issues and Implementing Best Practices for Prevention
Porosity in welding is a prevalent concern that frequently goes unnoticed up until it causes considerable troubles with the integrity of welds. In this discussion, we will certainly explore the key variables contributing to porosity development, analyze its destructive impacts on weld performance, and go over the finest practices that can be adopted to lessen porosity incident in welding processes.
Usual Reasons For Porosity
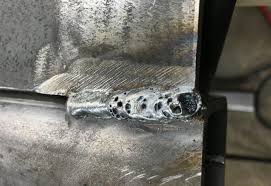
Utilizing unclean or wet filler materials can introduce pollutants right into the weld, adding to porosity concerns. To minimize these typical causes of porosity, complete cleaning of base metals, appropriate securing gas option, and adherence to optimum welding parameters are important practices in attaining premium, porosity-free welds.
Influence of Porosity on Weld Top Quality

The presence of porosity in welding can considerably jeopardize the structural stability and mechanical residential or commercial properties of bonded joints. Porosity develops gaps within the weld metal, deteriorating its overall stamina and load-bearing ability.
Welds with high porosity levels have a tendency to display reduced effect stamina and minimized capability to warp plastically prior to fracturing. Porosity can impede the weld's ability to properly transmit forces, leading to premature weld failing and potential safety hazards in important structures.
Best Practices for Porosity Prevention
To boost the architectural stability and quality of bonded joints, what specific measures can be carried out to minimize the incident of porosity during the welding process? Making use of the appropriate welding method for the certain product being bonded, such as readjusting the welding angle and gun position, can better stop porosity. Regular inspection of welds and prompt remediation of any kind of problems determined during the welding procedure are important find here practices to protect against porosity and produce high-grade welds.
Value of Correct Welding Methods
Implementing correct welding methods is critical in making certain the structural integrity and top quality of bonded joints, building on the foundation of reliable porosity avoidance measures. Welding techniques directly site here influence the total stamina and sturdiness of the bonded structure. One key element of proper welding methods is keeping the right warmth input. Too much warm can cause increased porosity because of the entrapment of gases in the weld pool. Alternatively, insufficient heat may cause insufficient combination, producing possible powerlessness in the joint. In addition, utilizing the suitable welding parameters, such as voltage, existing, and take a Read More Here trip speed, is vital for attaining audio welds with minimal porosity.
Moreover, the choice of welding procedure, whether it be MIG, TIG, or stick welding, must align with the certain requirements of the job to make certain optimum outcomes. Proper cleansing and preparation of the base metal, along with choosing the ideal filler material, are also important components of competent welding strategies. By adhering to these best techniques, welders can minimize the threat of porosity formation and generate high-grade, structurally sound welds.

Checking and Quality Assurance Steps
Quality control actions play a critical duty in confirming the integrity and dependability of welded joints. Evaluating procedures are vital to spot and prevent porosity in welding, making certain the stamina and sturdiness of the end product. Non-destructive testing methods such as ultrasonic screening, radiographic testing, and aesthetic inspection are frequently used to determine prospective flaws like porosity. These methods permit for the evaluation of weld quality without endangering the honesty of the joint. What is Porosity.
Post-weld evaluations, on the various other hand, examine the final weld for any type of defects, consisting of porosity, and verify that it fulfills specified standards. Executing an extensive quality control strategy that consists of thorough screening procedures and assessments is critical to reducing porosity problems and ensuring the overall top quality of welded joints.
Verdict
In final thought, porosity in welding can be a typical issue that influences the high quality of welds. By recognizing the common causes of porosity and implementing best techniques for prevention, such as correct welding strategies and testing steps, welders can guarantee excellent quality and dependable welds. It is important to prioritize prevention techniques to lessen the event of porosity and preserve the integrity of welded structures.
Report this page